Precast Promotes Innovation in Every Type of Project
August 20, 2016
From the Summer 2016 issue of Ascent Magazine.
The following is a portion of the full article.
By Craig A. Shutt
The plasticity, design flexibility, aesthetic versatility, resiliency, and economical effectiveness of precast concrete helps designers and contractors meet challenges and create striking buildings
Developers, architects, structural engineers, and contractors regularly confront challenges that impact their designs. Many times, they turn to precast concrete components to help them resolve these issues so they can create buildings with unique and distinctive elements while overcoming constraints in the site, budget, or schedule. As they push the envelope, precasters respond by using precast’s attributes to engineer solutions to meet those demands. High-performance precast concrete components offer ever-growing capabilities due to their versatility, efficiency, and resiliency. Each attribute offers multiple advantages that designers and contractors can emphasize to aid their needs. These benefits can be engineered to meet a variety of needs, and precasters continue to build on them and combine them to help create innovative structures. The following examples in diverse building categories show ways in which precast concrete was used to achieve unique designs with stringent requirements.
Medical Center Parking Structure
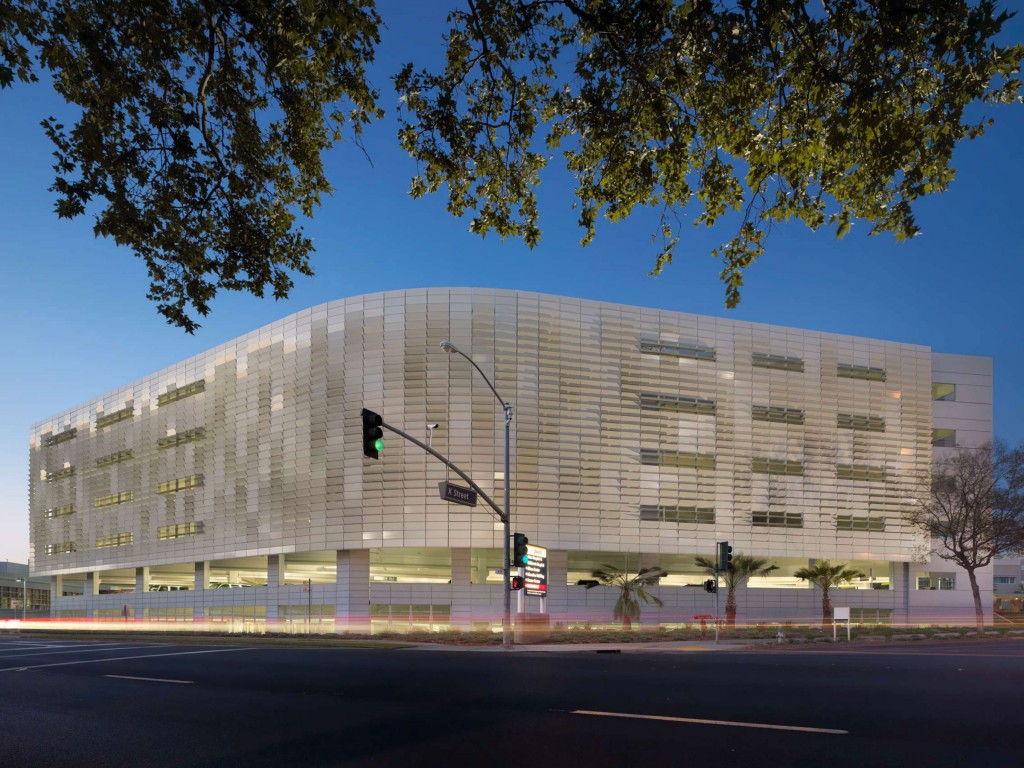
The new six-level, 400,000-square-foot parking structure at the gateway to the University of California at Davis Medical Center in Sacramento, Calif., features a precast concrete hybrid moment frame that allows the structure to self-right after a seismic event. A distinctive “lap-siding” design for spandrels provides visual interest while helping to keep the façade clean.
The new parking structure at the University of California, Davis’ Medical Center in Sacramento, Calif., was designed to meet the needs of an expanding population of patients and visitors to the center, an academic health center focused on advanced care, and new treatment options. To reflect this cutting-edge work, administrators wanted a design that expressed a contemporary feel that projected the center’s professional reputation while still meeting the facility’s functional needs, which included providing a structural system that could meet the area’s high-seismic needs.
To meet these goals for the six-level, 400,000-square-foot structure, designers chose a precast concrete structural system and architectural panels, along with poured floors. The framing system features a precast hybrid momentframe design that meets the seismic needs by uncoupling the connections so the building can self-right after a seismic event. For its aesthetic plan, architects created a modern appearance that features an integrally colored white architectural finish with lap-siding-shaped reveals emphasized by a series of metal panels attached to the entry. “Some parking structures are treated as utilitarian buildings and are hidden behind the main facility, but this one sits at the front of the medical center,” explains Matt Engleking, project manager at Clark Pacific, the precaster on the project. “Given its location, administrators wanted the structure to act as the center’s highly visible ‘front door’ while blending with the existing campus architectural style.”
Specifying precast concrete for the project was an easy choice, says Jason A. Silva, design principal at Dreyfuss + Blackford Architecture, the design architect on the project. “I’ve been a fan of precast concrete for a long time.” Silva has used the material on a variety of projects, including four in the past eight years. “This was the first time we could leverage the hybrid moment frame, which offers a lot of opportunities.”
‘It shows the ingenuity and talent of the designers when they can create a dynamic appearance that’s also efficiently produced and economical.’
A key advantage is the flexibility it offers. “I like to work with precast concrete as a kit of parts,” he explains. “It has a certain modularity and uniformity that helps guide the design. It can be something of a challenge to work within those constraints, but it’s also a benefit because it can help reduce the design to its fewest parts while creating an elegant solution. It doesn’t create any engineering challenges, and it provides a design approach that speaks to the process required to get there.” The economics also appeal to him. “If I can make the structure more efficient, I can put more of the budget into the finishes inside,” he explains. “Precast concrete comes with an architectural finish inherent in it, so it saves time and money by not having to apply those afterward, and it offers a high-quality appearance that’s very efficient. I can’t reduce my costs by removing the finish from the panels, so the finish is not part of the budget decisions, it’s part of the primary structure.” As a result, he achieves a much higher quality appearance than would be possible with other materials. “It requires diligence to maximize the appearance, but the options are unlimited,” he says. “It shows the ingenuity and talent of the designers when they can create a dynamic appearance that’s also efficiently produced and economical.”
The designers evaluated a cast-in-place structure, but the added finishing costs eliminated it from consideration. “A cast-in-place design would have required precast concrete panels hung from the exterior to match the surrounding buildings, so it didn’t make sense.”
Lap-Siding Profile Cast
The design plan used the appearance of lap siding as its influence, with a “shingling” shape that adds texture and visual interest. “The quality of the material really helped to achieve the look we wanted,” he says. The architect worked with Clark Pacific on a design-assist process to work out how the various pieces could be cast to maximize efficiency. They also worked out embeds into the panels for the array of metal louvers and aluminum panels attached to the concrete panels. “By working on a design-assist process, we could ensure continuity of the architectural style with the existing medical campus buildings,” says Engleking. Silva agrees. “We’ve worked well with them in the past, and we always invite them to give feedback and help create more efficiencies.” A key benefit of working closely from the beginning was the level of precision that could be provided, Silva says. Dimensions could be planned tightly, with the architect confident the components would fit closely. Reveals were added to spandrels alongside thin, horizontal openings to emphasize the horizontal nature of the parking structure, and other architectural accents were added as well. Metal louvers were focused on key points, including the entry, to direct visitors to the entrances clearly.
The campus palette focuses on four main materials, Silva explains: white precast concrete, off-white aluminum metal pieces for canopies and awnings, anodized aluminum, and green glass. The parking structure was designed to emphasize the first two especially. The horizontal rectangles created by the reveal pattern have an added benefit in their lap siding, which has each segment angling outward, with the one beneath indented behind it. That helps ensure the pure-white concrete mix will stay white, Silva says. “Cars in large parking structures generate soot, and it can settle into reveals. To minimize that concern and add more shadowlines, we added the lap form to prevent streaking after a rain.” Tops of the crash rails also slope inward to ensure no staining flows from the interior. “It was a challenging form for Clark Pacific to create, since it’s more complicated than traditional panels with reveals, but it achieved its goal,” Silva says. “The form works very efficiently and the quality we received was very high.”
Metal panels, mesh, and aluminum louvers were attached to the panels on façades facing the street. The louvers were designed with consideration for traffic, with each angled differently to diffuse headlight glare while creating a sense of movement from one set of louvers to the next. The embeds were placed and panels were installed smoothly. “They worked perfectly, just as intended,” Silva says. “They had a high level of accuracy.”
Hybrid Moment Frame
Seismic needs were met by the precast concrete hybrid moment frame. “I always advocate for the moment frame due to the open space it can provide while meeting seismic needs,” Silva says. “This is a 24-hour facility, with many visitors feeling very emotional as they arrive and depart. They need clear, open lines of sight for safety, security, and accessibility.” The interior was painted white to add to this. “The white concrete reduces the ability of dirt to cling to the walls and adds brightness.”
The benefit of the hybrid frame is that it uses the joints as a controllable focus for absorbing force and flexing with it, providing an easily inspected and repaired location after a seismic event. In other types of structures, that deformation can occur randomly and at an unknown point, producing time consuming and expensive inspection and repair processes.
The precast concrete moment-resistant frame absorbs seismic energy independent of the integrity of the structural members. The post-elastic performance concentrates in the connection region rather than a structural member. By combining both inelastic and elastic responses, minimal damage occurs to the moment frame, typically in the form of minor spalling. The benefits that result from this design include life-safety enhancements and economics, as well as open interiors through eliminating shear walls. The designers considered using double tees rather than cast-in-place floors, but the irregular shape of the parking structure and tight site made that design impractical. “We have a 180-foot ramp that had to be warped a little to fit the space, and it was too tight to make double tees work efficiently,” Silva explains. “In most situations, I would have used a total-precast concrete design.”
All of the components were delivered to the site and erected on a just-in-time basis, with trucks arriving and pieces being picked before the next truck arrived. “We could time trucks about 15 minutes apart, which really helped, as we had no staging area,” Silva says. “It eliminated the concern of having a pump truck sitting on site for days.” The crane was placed at the center of the footprint, and the structure was built out from the edges due to the tight site. “We were 30 feet from the hospital, with the property line on two sides and the hospital on the others,” Silva says. “We had no maneuvering room, so we stayed inside our footprint.”
Using precast and building rapidly in this fashion cut 2 months from the schedule, he estimates, and reduced the impact on the campus. “I advocate for this system whenever I have to build to the property line.” The project fulfills the University of California System’s standards for sustainable practices as well, incorporating energy-efficient and sustainable features. These include a photovoltaic power system, which provides 145 kW of power to the hospital and electric-vehicle charging stations. The result is a parking structure strategically located as a signature statement for the hospital campus that offers functional service and strong life-safety measures in case of a seismic event. “It very effectively showcases the functionality and aesthetic versatility of precast concrete,” Engleking says.
Silva agrees, to the point that he’s using precast concrete again on his next project, now underway at Sacramento State for an 1,800-car facility. “We have more room and a less complicated footprint, so it will be a total-precast concrete structure,” he says. “I’ve been considering some design ideas that will maximize the benefits of the precast concrete double-tees at the perimeter to add daylight to the interior. You’ll see those come to fruition on this new design.”